Unlike material removal methods such as milling and turning, a 3D printer does not waste material
|
|
Dear Industry Expert,
Unlike material removal methods such as milling and turning, a 3D printer does not waste material, because it only uses the amount of powder that actually needs to be melted to create the part. Virtually no manual post-processing is required, reduces tool costs. More... |
|
TOP STORY |
 |
|
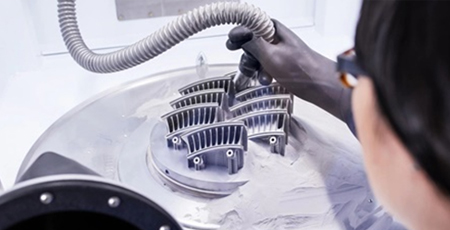 |
Sustainable production process for heat-resistant materials
TRUMPF demonstrated how 3D printing is manufacturing processes for heat-resistant materials. These materials often consist of the nickel-based alloy Inconel®, which can withstand temperatures of up to 1,000 degrees Celsius without deforming. Inconel® is used in applications such as gas turbines, combustion engines and heating systems, but it is difficult to machine using conventional methods. Milling tools often get stuck, snap off or lose their edge. It showed how Inconel® parts can be produced faster using 3D printing. More... |
|
TECHNICAL HIGHLIGHT |
 |
|
World’s largest multi-material 3D printing system now here
The KRAKEN is a research result from H2020 EU program capable of producing parts through Additive Manufacturing alternating material deposition with subtractive operations (layer-by-layer) within a maximum working area of 20m x 8m x 6m. Guaranteeing accuracy in large workspaces (100m2) is a challenge that Kraken has solved by integrating real time laser tracking technologies within the closed loop control of the robotic system.
More...
|
|
OPEN MIND offers CAM solution for 3Dprinting
OPEN MIND will present a groundbreaking addition to the hyperMILL® CAD/CAM suite at EMO: One of the world’s leading CAD/CAM solutions for satisfying the requirements of industrial 3D printing processes has been further complemented by hyperMILL ADDITIVE Manufacturing. hyperMILL® – together with this option will provide efficient hybrid processing with simultaneous additive and subtractive processing on one single machine. More...
|
|
Smart software for optimising lightweight structures
Four friends who, during more than four years of research at the Research Center for Additive Manufacturing (DMRC) of the University of Paderborn, came to an important realisation: industrial 3D printing offered many different possibilities for producing delicate but highly robust light metal components at low cost, yet there was a lack of suitable software. Manual data transfer into CAD formats was time-consuming and labour-intensive and left a lot of room for interpretation.
More...
|
|
Why use position indicators?
SIKO, manufacturer of industrial measurement and drive technology, expects the use of intelligent systems to continue growing in Southeast Asia (SEA), and is very confident of efficient adoption as well. “I think industrial customers in Southeast Asia are actually moving towards all these intelligent systems or what we call smart machines or smart factories,” said Jacky Tan, General Manager of SIKO Products Asia Pte Ltd. More...
|
|
Increasing productivity with the MILLTURN
The MILLTURN was at the centre stage for WFL at this year's EMO. Three demonstration models were on show during the trade fair from 16 to 21 September: an M30-G MILLTURN / 1800mm with automation cell, an M50-G MILLTURN / 3000mm with a focus on turbine blade machining and an M80X MILLTURN / 3000mm with an integrated diode laser. To complete the package, WFL has developed intelligent tools and integrated sensors for the MILLTURN machines. More...
|
|
The digital twin has become real
In the construction of complex machine tools, engineering and manufacturing often used to be two successive processes. GEORG, as pilot customer of Siemens, presents, as a first, digital twins of two of its machine tools. This makes Georg a pioneer in implementing in practice the next stage of the digital transformation in machine tools, using the new CNC generation “Sinumerik ONE”. More...
|
|
|
|
|
|
|
|