A new tool concept allows the metal cutting of even high dimensions
|
|
Dear Industry Expert,
Tool manufacturers have been successfully implementing WALTER's two-in-one concept in production for 17 years now. But what exactly is behind this concept which competitors have now even been trying to copy? |
|
|
TOP STORY |
 |
|
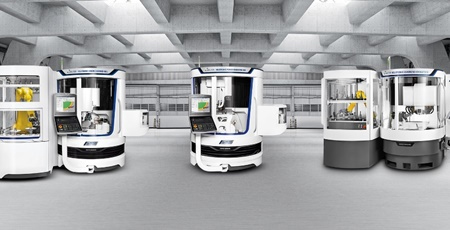 |
Eroding and grinding using one machine
From a production viewpoint, the two-in-one concept means that users can completely erode tools and also completely grind tools using one and the same machine. What is more, and this is one of the key advantages, both processing methods can be used on one and the same tool without the time-consuming step of switching to a second machine. This is especially necessary and more efficient in the case of modern PCD tools where the carbide blank already has soldered PCD. The ability to erode, grind or even do both in one clamping operation gives the user an unparalleled level of flexibility in their production processes. More... |
|
TECHNICAL HIGHLIGHT |
 |
|
Milling cutters for extremely long service life
In the automotive industry, steel materials are increasingly being replaced by aluminium alloys, particularly when it comes to sports models. This helps manufacturers to work towards their efficiency targets, as well as requirements for dynamics that they have set themselves. Although aluminium is good to work with when it comes to machining, the material does have its drawbacks, which tool developers try to minimise using specially adapted tool systems. More...
|
|
Sealed miniature clamping module with high pull-down force
SCHUNK has developed a completely sealed miniature clamping module specifically for compact applications in the metal cutting industry, assembly and handling, as well as for the measurement technology. It combines compact dimensions, high pull-down and holding forces, a high dimensional stability, and a high repeat accuracy of < 0.005 mm. The VERO-S NSE mikro 49-13 achieves high pull-down forces despite the compact dimensions. More...
|
|
|
New generation of HPC end mills for universal use
The newly developed high-performance end mill 35402 from TOOL FACTORY Cutting Tool Solutions GmbH in Burscheid impress with their long tool life and process reliability. For the market launch, machinists can test the milling cutters in a set with a 20 % additional discount. TOOL FACTORY presents the newly developed HPC cutters of the 35402 series in its Professional Line and enters a new performance class in universal applications. More...
|
|
|
Maximum metal removal
Imagine burying a roughing tool in a block of Ti-6Al-4V titanium and ripping away more than 1000 cm3 (61 cubic inches) of material in just one minute. If you’d been at a recent test of Kennametal’s new HARVI™ Ultra 8X helical milling cutter, you’d have seen exactly that. Tim Marshall, senior global product manager for indexable milling, tested the HARVI Ultra 8X with a variety of customers, pushing the limits of the new. More...
|
|
|
Faster programming, more efficient cutting
Enhancements are to programming tasks, and also to make machining quicker and simpler. The new 3D and 5-axis corner rest material strategies guarantee the efficient machining of rest material in corners. What’s even more promising is that optional modules – hyperMILL® ADDITIVE Manufacturing and hyperMILL® VIRTUAL Machining – offer groundbreaking technology, simulation, optimization, and connectivity solutions consistent with key directions of modern manufacturing. More...
|
|
Highly productive grinding of eccentric shafts for robot joints
Today, progressive automation in production and manufacturing is primarily driven forward by the use of industrial robots in an increasing number of industries. More than 1.7 million new robots, designed for handling, assembly or processing workpieces, will be installed by the year 2020. SCHAUDT presented its compact and highly versatile ShaftGrind S cylindrical grinding machine with an integrated robot. More...
|
|
|
|
|
|
|
|