Transmissions for electric cars are much simpler in design than for conventional combustion engines
|
|
Dear Industry Expert,
Transmissions for electric cars are much simpler in design than for conventional combustion engines, but place far higher demands on the manufacturing precision of the gears used. Thanks to completely new procedures for quality assurance directly in the final machining process, which is gear grinding, these specifications can also be met in series production. |
|
TOP STORY |
 |
|
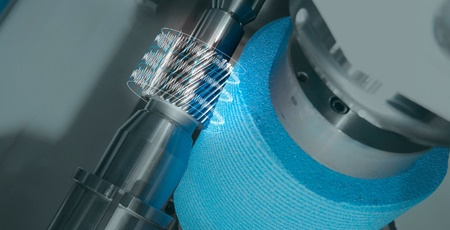 |
Intelligent generating grinding
All-electric vehicle drives usually make do with two-stage, non-shiftable transmissions. You would have thought that this would greatly simplify production. After all, this type of transmission design has just four gears, distributed between the drive shaft, the second stage with fixed gear and intermediate shaft, and the axle drive gear. But
in reality, it’s not that simple: first of all, engine speeds are much higher for the e-drive than for combustion engines, at up to 16,000 rpm. This means electric motors
deliver an almost constant torque over a wide speed range. Unlike combustion engines, it is applied to the transmission right from zero speed.
More... |
|
|
Gear solutions for e-mobility
New drive technologies in electric mobility are changing the requirements for gears and therefore also for the quality of the tooth flank surfaces. Manufacturers of gears have to adapt their manufacturing process accordingly. It’s good to be able to rely on a technology partner with expertise covering the entire range of production processes and technologies, which enables them to find suitable solutions even for special challenges. More...
|
|
Hard-coated brake discs become a hot topic
Alongside tire wear and the combustion of fossil fuels, brake abrasion contributes to the high particulate pollution caused by vehicles with combustion engines and electric or hybrid drives. The automotive industry needs innovative technical solutions to reduce this contamination. JUNKER develops innovative and unique process for hard-coated brake disc production. This innovative hard coating process leads to high-quality anti-corrosion and wear-resistance. More...
|
|
Electric cars in the fast lane
Electric vehicles are gaining strong momentum in the automotive market. The AlixPartners analysis reveals “that investment in electromobility will grow much faster by 2025 than expected last year”—globally by plus 41 percent, and in Europe by plus 52 percent. High growth rates in new registrations are already driving the cable and wire industry to invest in ever more modern technology. Electromobility is undoubtedly electrifying suppliers. More...
|
|
How digital twins can save mobility market from expensive errors
Digital twins have accelerated innovation and unlocked new business models in the mobility sector, according to Frost & Sullivan's latest analysis on digital twins in global mobility. DTs assist OEMs in designing and validating new products and features in the virtual environment before creating a physical prototype. Additionally, the COVID-19 pandemic and increasing digitalization have highlighted the importance of DTs as they enable RMC in manufacturing.
More...
|
|
|
|
Laser applications for electromobility
The importance of laser welding in car manufacturing has been increasing significantly for years, and not just in car body production. Many components under the hood or, more accurately, in the drive train – benefit from the precise and fast process. Laser welding is likewise increasingly used in the manufacture of electric motors, for example with copper or aluminum compounds, especially in the electric drive and in the battery. More...
|
|
|
|
|
|
|
|